Backflow Testing is a critical part of keeping your water clean. It also keeps you in compliance with local backflow regulations.
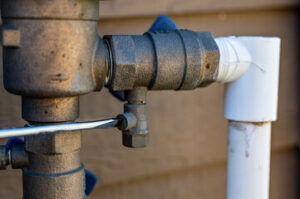
Generally, the standard testing procedure requires the backflow preventer to be temporarily disconnected from your water supply. That’s why letting a licensed plumber handle your backflow testing is best.
A backflow preventer is a device that can stop dirty water from reverse flow into clean lines. This dirty water can contain human waste, chemicals and other contaminants that are dangerous to your health. It can also cause property damage when it travels through your pipes and back into your building, causing flooding, mold and other issues. Local authorities and plumbing codes require you to test your backflow prevention system on a regular basis to ensure it works as designed. Failing to do so could result in a fine or having your water temporarily disconnected.
The testing process involves using valves on your backflow preventer to simulate a backflow event. This includes closing the test valves and checking for gauge movements, water leaks and other clear signs of backflow. You will need to have a certified plumber like Kiddco Plumbing Inc perform this test on your behalf. They will have access to the proper equipment and knowledge of the specific procedures required for each type of backflow testing device.
During the backflow testing process, a plumber will examine your valves and pressure regulators. They will also inspect the overall function and direction of water flow through your plumbing. They will check for any pressure imbalances, which are the most common cause of backflow problems. They may even conduct a siphoning test, which can mimic backflow and see how your plumbing reacts.
Once the backflow testing professional has completed their inspection, they will use a backflow device to perform the actual test. This is a procedure that requires you to temporarily disconnect your water supply, but it is one of the most important parts of testing your backflow preventer. If you don’t have a certified plumber that can perform this part of the test, you should contact the one who did your initial backflow testing.
The tester will follow the guidelines provided by the manufacturer of your backflow prevention device to determine if backflow is present and to identify what caused it. This will involve closing the test valves and observing how the gauge moves, as well as examining each of the valve components. The tester will then write the results in their report.
Relief Valve
A backflow preventer’s function is to ensure water goes where it should. This means that it keeps backsiphonage from occurring, which can cause backflow in your drinking and cooking water. This interaction can result in contamination, illness, and back pressure that damages pipes and other components in your building. That is why it’s important to have your backflow preventers tested and properly maintained by a professional.
There are specific guidelines that your plumbing expert must comply with before they can conduct a backflow test. To start, they need to turn off your backflow device’s water service. They will then open and close all valves on the test equipment, while watching for changes in gauge movement, water leaks and other clear signs that the device is working as intended.
One of the most crucial tests during a backflow test is the check valve’s relief valve. The relief valve is designed to release pressure in the event that the assembly fails. It is required by code to be rated at least 2.0 psi less than the inlet pressure upstream of the first check. It is also required to be made of an elastomer that will work with the fluid and in its expected operating temperature range. Common elastomers used in this type of application are Buna-N and EPDM.
The tester will also be looking to see if the test assembly is working by opening and closing test port number four. If it is leaking or discharges water, the first and second check are either dirty or not functioning correctly. This means that the assembly must be cleaned or replaced.
The backflow prevention system must be tested every year to guarantee that it is still functioning as intended. If the system is not functioning as it should be, your plumber can make adjustments and perform repairs to restore proper operation. They will then submit the test report to NYC Department of Environmental Protection (DEP). The DEP will review and approve the report, and you can resume water service.
Test Cocks
Backflow Testing is the annual inspection (required by the State of Colorado) of the backflow preventers installed in your cross-connections to ensure they are working properly. Backflow testing is a vital step in keeping your water clean and safe. During the test, all check valves, relief valves, air inlet valves, and shut off valves are tested to ensure they’re functioning correctly.
The main function of a backflow preventer is to keep the flow of water going in one direction, so it can’t be reversed into your piping system. They are often associated with fire protection systems because of the sprinklers that explode when you pull the alarm, but backflow prevention devices are also used for residential plumbing and even lawn irrigation.
During the backflow test, these preventers are tested to make sure they can’t be reversed and that they protect your home’s clean water supply. The backflow testing process involves removing the hoses from the assembly, shutting off the upstream (number 1) and downstream (number 2) shut off valves, and then hooking up your backflow test kit. You’ll want to make sure that your hoses are clean and free of any debris before connecting them to the assembly.
The backflow tester will attach the hoses to the test cocks, then connect the pressure gauge. After the pressure test, the hoses are hooked up again and the assembly is flushed for debris. You’ll also want to ensure that the assembly isn’t leaking by checking that the test cocks are still sealed. If a test cock leaks or isn’t sealed, the device won’t pass the test.
The type of backflow prevention device that you need depends on what kind of work is being done in your building. PVB assemblies, which are usually used for lawn irrigation, are the least expensive of all whole-system backflow preventers. They are relatively simple in design and easy to maintain and repair. Double check assemblies, which are typically used for fire protection systems, feature a redundancy in which two independently operating spring-loaded check valves are located inside a single valve body. These assemblies have an inlet (upstream) shutoff valve, four test cocks, and an outlet (downstream) shutoff valve.
Pressure Gauge
Backflow Assembly Testers (BAT) use the pressure gauge as part of their test kit to measure the function of backflow prevention assemblies. The pressure gauge is connected to the test cocks on the backflow assembly with long hoses, and the tester reads the gauge during a field test. The gauge can be either analog or digital and is made from various materials. Gauges also come with a variety of features including:
The type of media being tested will dictate the gauge that is best suited for the application. For example, food grade pressure gauges must be exceptionally hygienic and are typically made of stainless steel grade 316. They are designed to withstand impacts, vibrations, temperature extremes and other hazardous conditions. Other factors to consider when choosing a gauge include its size and the way it is mounted. The gauge case is available in many different materials and shapes including thermoplastic, aluminum or stainless steel. Some models feature a solid front which creates a partition with minimal openings between the pressure element and window to reduce the risk of accidental rupture. Gauges with a solid front are more expensive but offer superior protection.
Most gauges have a built-in overrange feature which prevents the bellows from being squeezed too hard. The overrange feature is typically accomplished by an internal stop mechanism that keeps the traveling parts inside the gauge from moving beyond their normal range. This is important so that the pressure generated from a backflow preventer test or by a sudden pressure spike does not cause damage to the gauge or its components.
Like any instrument or tool, the gauge must be inspected and certified annually. This inspection includes simulating a backflow test to ensure the gauge is functioning properly. If the backflow test gauge fails this inspection, a backflow gauge calibration must take place to restore its accuracy. Keeping up with these inspections will help maintain water safety standards, and ensure the backflow test kits are providing accurate and trustworthy results.